Polished Concrete Countertops vs. Granite and Quartz vs Epoxy: A Comparison
Did you know the average kitchen surface endures 15,000 impacts yearly? Choosing the right material isn’t just about looks—it’s about lasting performance. This guide explores how modern engineered options stack up against traditional favorites, giving you clarity in a crowded market.
Modern surfaces blend strength and style through smart engineering. For example, professional-grade mixes combine cement with aggregates and sand, creating a matrix stronger than individual parts. Regional stone variations add unique character, making each installation distinct.
Durability varies wildly between materials. While granite resists scratches, epoxy offers seamless designs. Quartz provides consistency, but lacks the organic charm of natural elements. Understanding these trade-offs helps you match features to your lifestyle.
Key Takeaways
- Compare durability factors like scratch resistance and impact tolerance across materials
- Learn how cement-aggregate mixes create stronger surfaces than pure components
- Discover how local stone sources influence color and texture variations
- Evaluate maintenance needs for different finishes in high-use spaces
- Identify design flexibility options for kitchens and bathrooms
Overview of Popular Countertop Materials
Homeowners today want surfaces that balance practicality with personal style. Let’s break down how leading options differ in construction and visual appeal.
Material Composition and Durability
Engineered surfaces start with specialized formulas. A 5000 psi mix combines cement with locally sourced aggregate , creating dense slabs that gain strength over time . This contrasts with granite’s natural mineral structure and quartz’s resin-bound design.
Epoxy coatings sit atop existing surface s as thin decorative layers. While durable, they lack the thermal mass of stone-based materials. Proper sealing determines longevity – natural stones need regular treatment, while engineered options resist stains better.
Aesthetic Differences and Design Options
Your finish choices define the space’s character. Exposed aggregates create textured looks you can’t replicate with manufactured slabs. Integral color pigments produce consistent hues, while polishing depth adjustments reveal different visual layers.
Granite offers earth-toned variations, whereas quartz delivers predictable patterns. Epoxy allows metallic accents but feels less substantial. Regional stone sources mean your surface could showcase local geology through visible mineral deposits.
The Process of Creating Polished Concrete Countertops
Crafting durable surfaces requires precision at every stage. Specialized techniques transform raw materials into functional art, blending technical skill with creative vision.
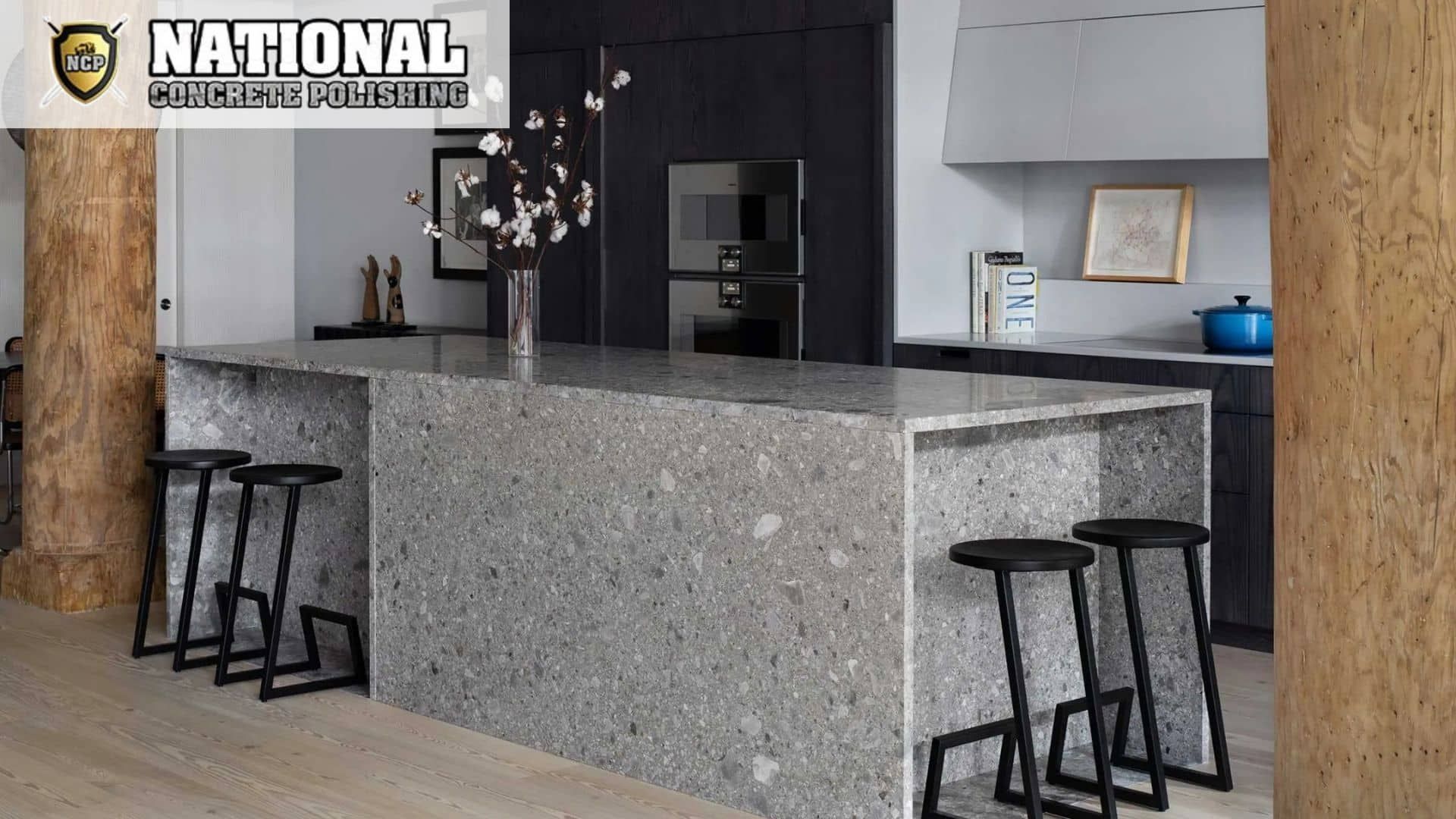
Preparing the Mix and Casting Techniques
Your project starts with forms built from foam rails or melamine sheets. The mix combines cement, sand, and aggregates in exact ratios – typically 5000 psi strength for lasting performance. Pour the blend upside-down, as the form’s base becomes your visible surface .
Imperfections in the mold transfer directly to the finished piece. Use templates to ensure precise edges and openings. Let the material cure 1-3 days before polishing – longer waits increase hardness but reduce aggregate exposure.
Wet Polishing and Grit Progression Explained
Begin with 50-grit diamond pads on a wet polisher , working through seven stages up to 3000-grit. Each step removes scratches from the previous grit , while the water feed prevents overheating. Maintain circular motions and steady pressure for uniform results.
- Coarse grinding (50-200 grit): Reveals aggregate texture
- Medium refinement (400-800 grit): Smooths scratches
- Fine polishing (1500-3000 grit): Creates mirror-like shine
Essential Safety Measures and Tool Requirements
Your tools must include a variable-speed polisher, diamond pads, and water supply. Wear goggles, gloves, and respirators – silica dust poses serious health risks. The machine’s 4-5” backer pad ensures proper contact with the surface during each polishing phase.
Seal the finished piece promptly. Proper technique preserves both your safety and the material’s longevity, making every step in the guide non-negotiable.
Polished Concrete Countertops vs. Granite, Quartz, and Epoxy Finishes
Selecting the ideal surface involves balancing aesthetics with practical needs. Each material brings distinct advantages and challenges that impact daily use and long-term satisfaction.
Material Strengths and Limitations
Customization options vary widely across materials. Engineered options let you choose integral color pigments and decorative aggregates for unique patterns. Natural stone offers organic beauty but limited design control.
Heat resistance tests reveal critical differences. Some surfaces handle hot pans effortlessly, while others risk permanent marks. Always use trivets for materials prone to thermal damage.
Feature | Engineered | Granite | Quartz | Epoxy |
---|---|---|---|---|
Custom Designs | Unlimited | Limited | Moderate | High |
Sealing Frequency | 2-3 years | Annual | None | As needed |
Repairability | High | Low | Very Low | Moderate |
Sustaining Your Investment
Proper care extends your surface ‘s lifespan. Use penetrating sealer s like Z Siacryl 14 for high-gloss finishes – they protect without altering texture. Counter-Shine products add extra protection for busy kitchens.
Address imperfections early to prevent worsening. Light scratches on some materials can be buffed out, while others may need professional attention. Always follow manufacturer guidelines for cleaning products.
Design, Execution, and Local Considerations in South Florida
South Florida’s tropical climate demands unique strategies for successful installations. High humidity and rapid temperature changes directly impact material behavior, requiring adjustments at every stage of the process .
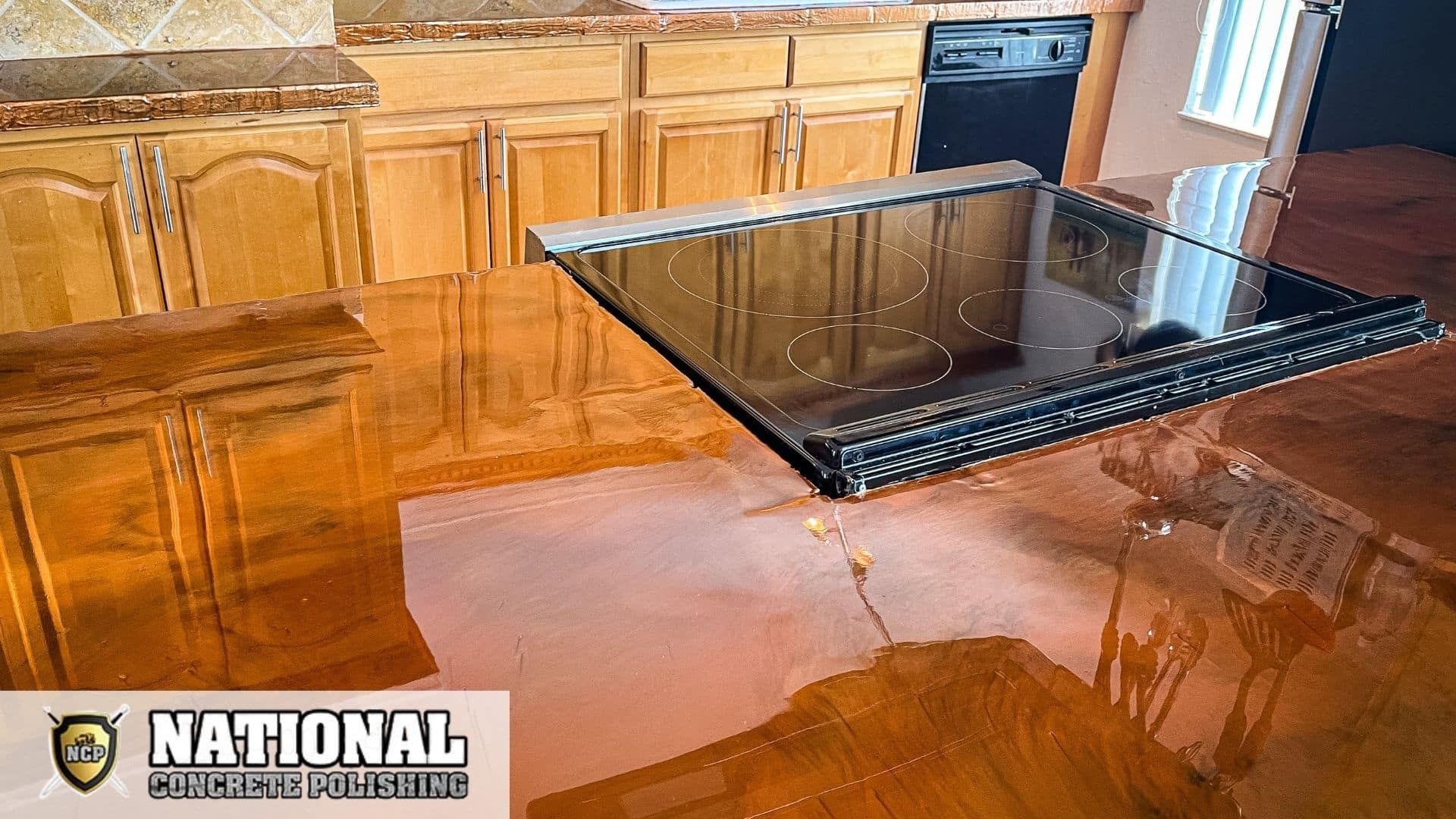
Insights from Industry Experts and Real-World Applications
Local contractors like National Concrete Polishing emphasize morning pours. This avoids afternoon thunderstorms that disrupt curing time . Complex designs, such as waterfall edges, need precise templates to prevent costly rework.
Aggregate choice matters in coastal zones. Crushed coral or coquina blends withstand salt air better than standard mixes. Always test local sand and aggregate combinations before full-scale projects.
Adapting Techniques for South Florida’s Climate
Adjust your slurry mix ratios – higher cement content compensates for humidity slowing hydration. Apply filler paste during 400-grit polishing to seal pores before final sealing.
- Extend curing protection with damp burlap for 72+ hours
- Use dehumidifiers in indoor workspaces during rainy seasons
- Schedule installations between November-April for stable conditions
DIY attempts often fail due to slab movement during curing. Professionals use reinforced molds and climate-controlled transport to ensure flawless finish es. For lasting results, trust specialists who understand regional challenges.
Conclusion
Your journey through material comparisons reveals how specialized techniques shape lasting surfaces. The right finish balances beauty with resilience, whether you prioritize seamless designs or natural textures.
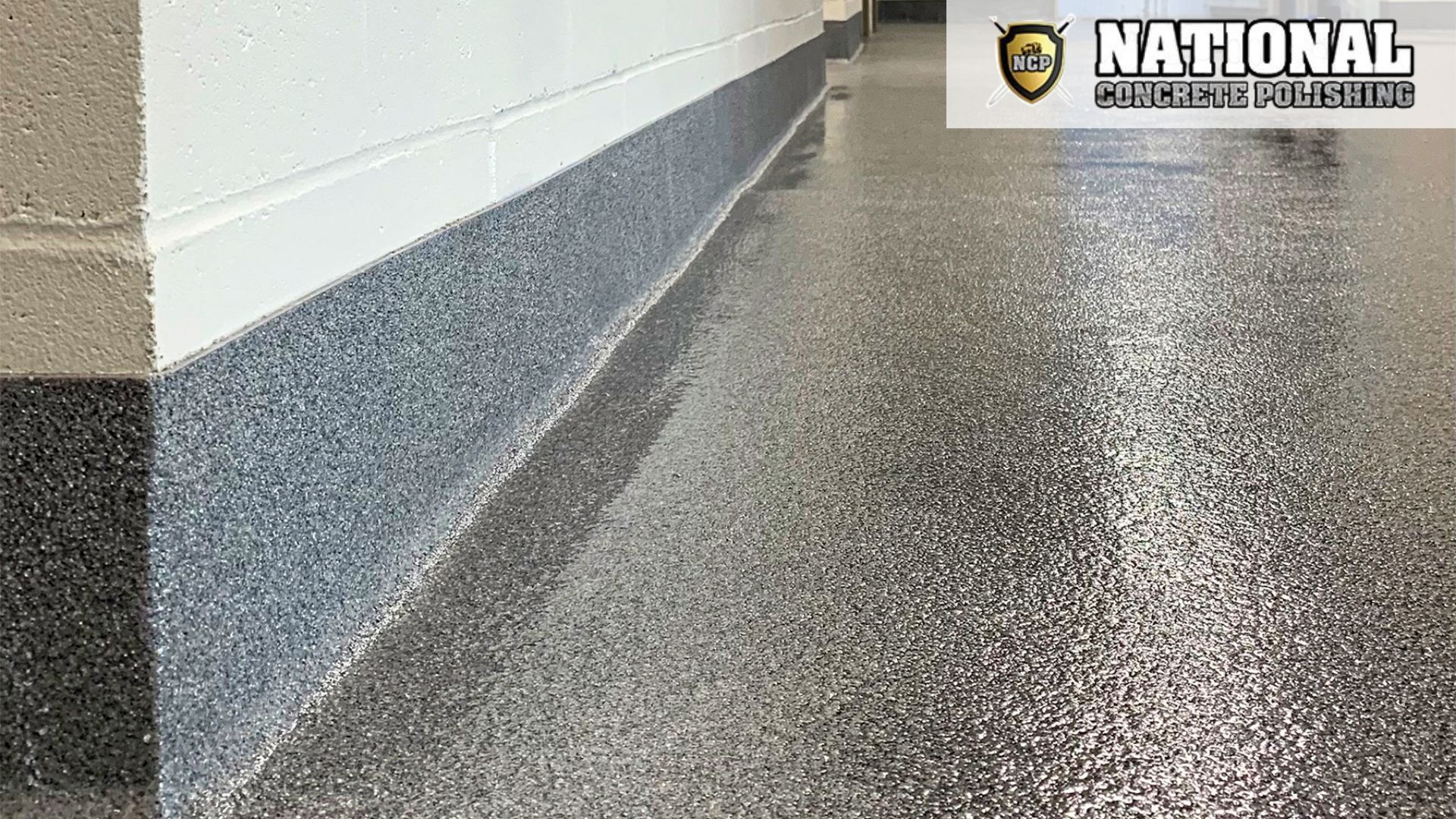
For South Florida residents, climate-smart execution matters. Humidity-resistant slurry mixes and precise polishing stages ensure surfaces withstand tropical conditions. Professionals like National Concrete Polishing (+1 877-661-7562) use localized methods to prevent imperfections caused by rapid curing shifts.
Quality tools and safety protocols transform raw materials into refined installations. From initial sand -cement blends to final sealer applications, each step demands attention. Proper grit progression removes slurry residue while revealing your chosen aggregates.
Your project’s success hinges on matching process knowledge with realistic timelines. While DIY approaches teach valuable skills, complex pours often benefit from expert hands. Let this guide steer your decisions toward surfaces that reflect both practicality and personality.
FAQ
How do polished surfaces compare to granite or quartz in terms of durability?
While granite and quartz are highly durable, polished options made from specialized mixes can match their strength. However, materials like epoxy may scratch more easily under heavy use. Each choice depends on your lifestyle and maintenance preferences.
What steps are involved in achieving a smooth finish during the polishing process?
A wet polisher with diamond-embedded pads is used, starting with coarse grit (50-100) to remove imperfections. Progressively finer grits (up to 3,000) refine the surface, followed by a densifier and sealer to lock in the shine and protect against stains.
Are there climate-specific challenges when installing these surfaces in South Florida?
High humidity and temperature fluctuations can affect curing times. Experts recommend using additives to slow drying and prevent cracking. Proper sealing is also critical to guard against moisture absorption in coastal environments.
Can you customize the color or texture during the mixing phase?
Yes, pigments or decorative aggregates like glass or stone can be added to the mix. For consistent results, work with a professional to balance aesthetic goals with structural integrity, especially in high-traffic areas.
What safety gear is essential when working with wet polishing tools?
Always wear OSHA-approved goggles, a respirator mask, and waterproof gloves. A GFCI outlet should power the polisher to prevent electrical hazards, and nonslip footwear is advised to avoid accidents from slurry buildup.
How does long-term maintenance differ between epoxy and other materials?
Epoxy requires periodic resealing to prevent yellowing from UV exposure. Natural stone alternatives need occasional impregnating sealers, while polished surfaces benefit from pH-neutral cleaners and reapplying topical protectors every 1-2 years.